Reuse saves $9M for Port Reconstruction
South Carolina Ports Authority
Charleston, South Carolina
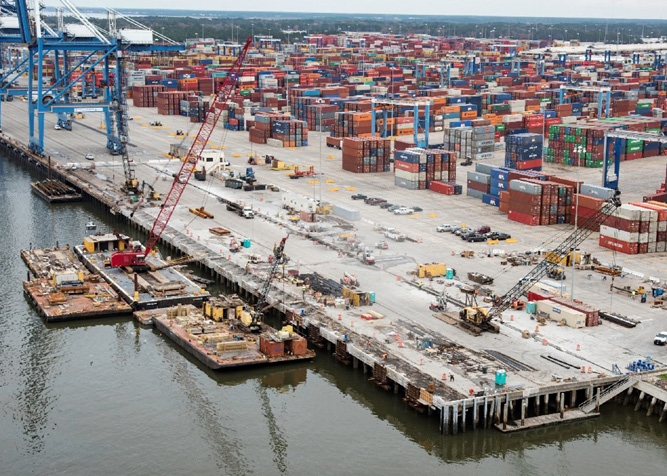
Scope of Foundation Work
Technology used, reason for the reuse:
Starting in 2015, the port of Charleston underwent a major upgrade to accommodate larger container vessels. The larger vessels require larger cranes with significant increases in foundation loading. Reuse of existing 18- and 24-inch square prestressed concrete piles was selected from the project initiation to reduce the cost of new foundations and limit the construction duration and corresponding impact on port activities.
Methodology to determine existing capacity:
The existing piles are driven through soft clay into the Cooper Marl
formation, where the piles develop most of their capacity through skin friction. Piles driven in the Cooper Marl formation are known to exhibit considerable pile setup, but most setup information is based on restrikes performed within weeks of initial driving. For the port upgrade, with 20- to 30-year old piles, the setup was hypothesized to be even greater. The project team performed dynamic tests on two piles during restrikes.
Retrofit construction activities conducted:
The existing piles were not retrofitted, but new piles were added to the port structure to increase the total capacity.
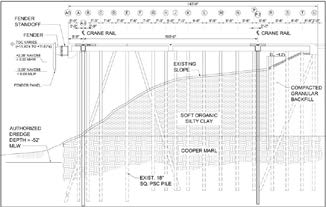
Conclusions
Cost savings:
Compared to initial estimates, results of the dynamic tests increased the allowable pile bearing resistance by 60 to 120 percent for the 18-inch piles and 40 to 90 percent for the 24-inch piles. The corresponding reduction in the number of required new piles produced considerable benefits. The direct foundation cost savings were estimated to be $9M. In addition, the construction schedule was shortened by 6 months, which results in valuable indirect savings considering the economic impact of disrupting port activities. These massive savings were achieved through a testing program that cost less than $300,000.
Three cost saving statistics:
- 1. $9M in direct savings.
- 2. Construction time savings of 6 months.
- 3. The in-situ testing program cost less than $300,000.
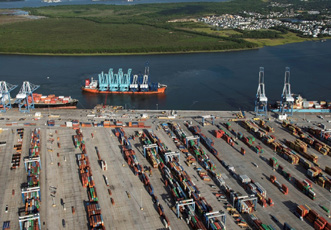
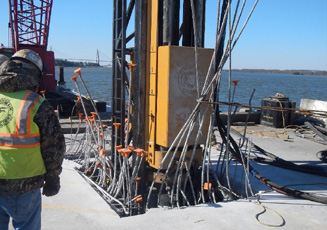
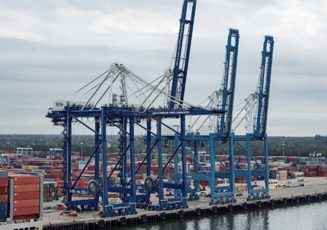