Carbon Footprint Reduction for River Wall Renovation
Author: Patrick IJnsen, Van ’t Hek Group
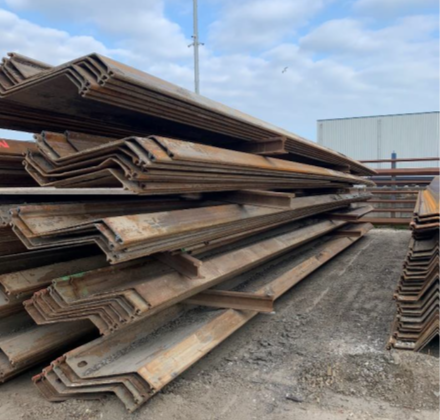
Van Halteren Infra (part of Van ’t Hek Group) was awarded the contract for a river wall replacement in the Dutch historical town of Schipluiden. The bid selection criteria included, best value for money, lowest life cycle cost and best price. The contractor’s plan to reuse steel sheet piles to provide a massive carbon footprint reduction made the bid successful.
The Challenges
An important step in carbon footprint reduction for steel foundation elements is the recycling of scrap steel as main raw material for hot-rolled steel sheet piles. However, the contractor went one step further and used previously used steel sheet piles as permanent elements in the new river wall, resulting in a carbon reduction of approximately 900 t CO2e.
Because the project was in a historical town, the sheet piles had to be installed without any vibration and with the least nuisance possible. Installing steel sheet piles with a sheet pile press sets the requirements for quality and tolerance for the steel sheet piles even higher.
The Solution
Although a procedure for implementation of reused steel elements is not yet covered in European Standards (Eurocode) or in Dutch Standards (NEN), Dutch National Guidelines on sheet pile design suggest a higher safety factor. But since the original material certificates were available, the pile shapes were still within the original tolerances and no damage was observed during a careful visual inspection, these elements were accepted and the higher safety factor was waived.
The Results
By accepting the contractor’s proposal to reuse sheet piles, the municipality not only saved money, but also reduced the carbon footprint of the project by 43%. In addition, the new river wall was constructed in a historical center without any damage and meeting all flood safety requirements.
Total carbon emissions in terms of greenhouse gas (GHG) CO2 equivalents for the reused sheet pile solution was 900 t CO2e. Other carbon footprint reduction measures used on the project include the use of hydrated vegetable oil (HVO) 100 diesel for construction
(110 t CO2e), use of green energy for all electric grid connection on the construction site instead of diesel fueled power generators (6.2 t CO2e) and the use of concrete with recycle aggregate and partial cement recycling (1.5 t CO2e).
The carbon emissions that were saved on this project are equivalent to the energy needed to drive an average car for 2,052,000 miles.
Use the EFFC/DFI Carbon Calculator and the EPA’s carbon equivalency tool (https://www.epa.gov/energy/greenhouse-gas-equivalencies-calculator) to figure out the impact of your carbon-reducing efforts on your next project!
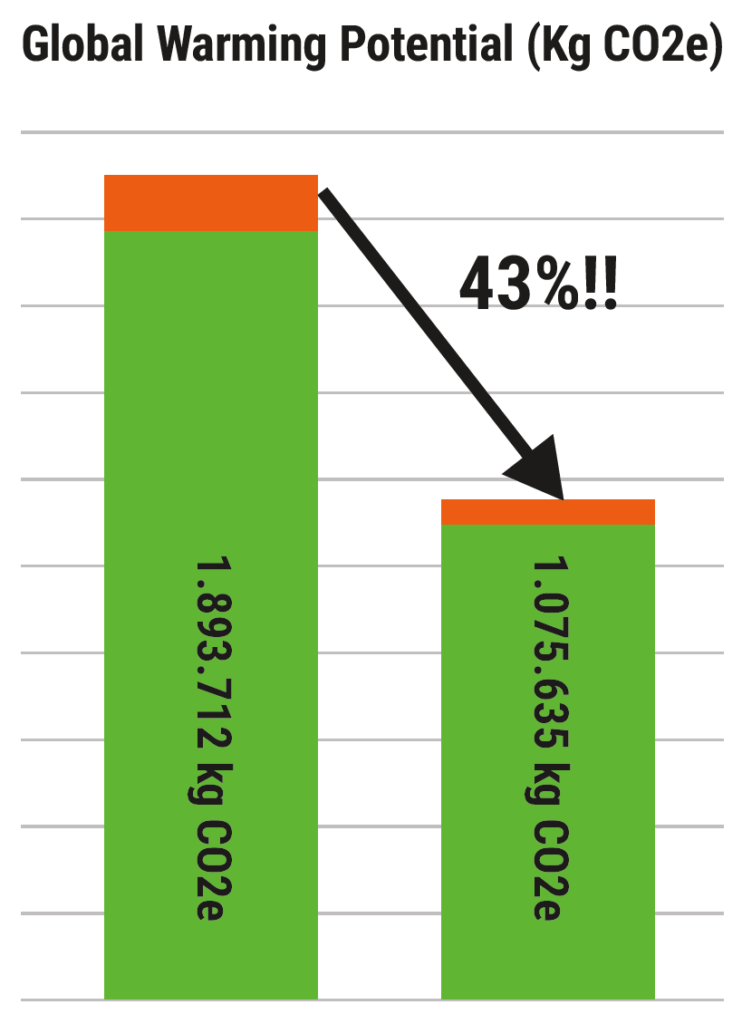