Saving Water in Spoils Separation
Author: Brandon Connolly, Stage 3 Separation
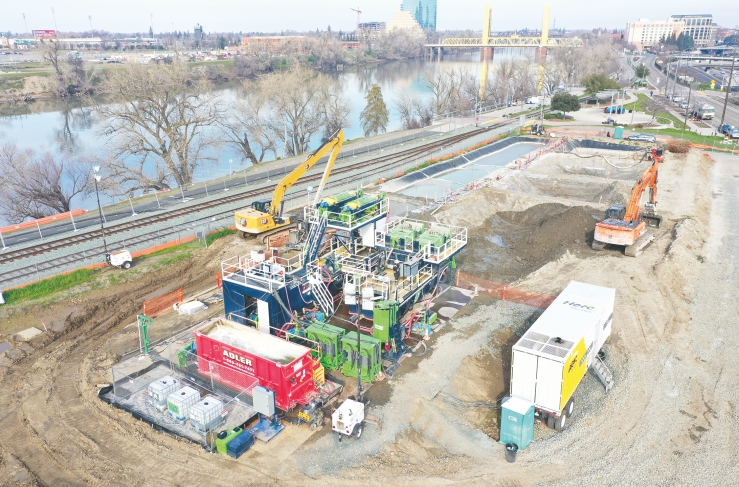
The Challenge
The Sacramento River East Levee Contract 2 (SREL 2), a U.S. Army Corps of Engineers project in Sacramento, California, awarded a contract to process jet grout spoils. A standard jet grout cutoff wall project would utilize large earthen pits, built exclusively for the purpose of dumping jet grout spoils. These would be allowed to harden and set over time. Then they would be excavated as solid jet grout spoils and sent to disposal with the pit then reused. The process of dumping, hardening and excavating a single pit can take up to several days, therefore a single project requires multiple pits to ensure continuous operations. Most of the water used in a jet grout cutoff wall is considered “single use.” The wastewater from this process is often high in pH and requires additional processing at a wastewater facility before it is considered safe for environmental release.
Because the work area in Sacramento did not have sufficient space to build jet grout spoil pits, an alternative solution was required. The alternative would need to be capable of processing 100% of the spoils from the jet grouting operation and providing a stackable dry solid that would be accepted at the local disposal. While sustainability was not the primary driver in the solution it was a very important secondary benefit.
The Solution
The contractor’s jet grout spoils system, along with its prescribed chemistry, were deployed to the project. The system received contaminated grout spoils from the jet grouting operation and separated the free water from the jet grout solids. This chemistry was added to the process at different points not only to improve the separation capabilities of the system, but also help remediate any contamination in the recovered water. This solution allowed for continuous jet grouting operations without the need to wait for spoils to solidify in pits. It also allowed recovered water to be reused in the jet grouting process. At the end of the project the jet grout water was pure enough to discharge into the sanitary sewer rather than hauled to a treatment plant, as is typically the case.
The Results
By utilizing this particular jet grout spoils system, the customer not only improved its uptime efficiency and reduced overall downtime, but also impacted the carbon footprint of the job by reducing the number of dump trucks and vacuum trucks by 40%.
Sustainability in industry should not only be measured in carbon footprint, however, and should also concern water management practices. The separation jet grout spoils system used on the Sacramento project recovered more than 2,160,000 gal (8,200,000 L) of water, which was reused in the jet grouting process and eventually discharged at the local sanitary sewer for reuse by the general population. This is the equivalent of at least 51,000 full bathtubs or three and a half Olympic swimming pools!
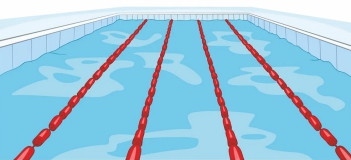